Technical
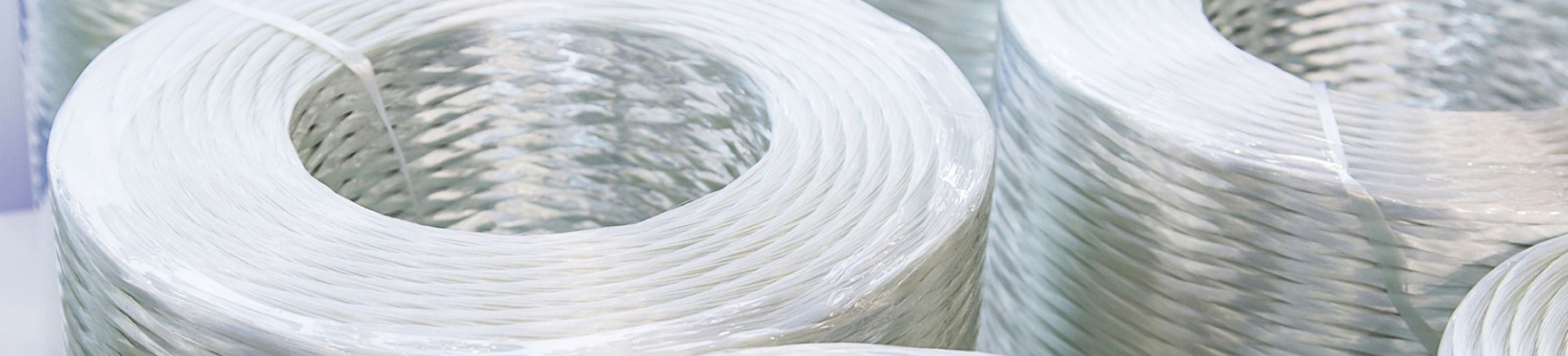
RF equipment for technical
Stalam’s RF equipment are “the standard” for the rapid and efficient drying of glass fibres, natural latex and SBR foams, medical PU foams, felts and other non-wovens. Stalam has also developed specific RF equipment to carry out innovative thermal processes such as the ribbonisation of glass fibres and the vulcanisation of latex foams.
The Radio Frequency drying process is endogenous (heat is generated directly within the wet product and not slowly transferred from an outside heat source), Xive (the RF energy is absorbed by the water inside the product and not by the product itself) and controlled (the amount of energy transferred to the product can be dosed accurately).
Thanks to these features, the RF drying of technical-textiles and non-wovens after various wet treatments like washing, padding, dyeing, wet spinning, wet casting, foaming, felting, impregnating, coating, etc. has many advantages compared to the conventional drying technologies based on heat transfer – above all: higher energy efficiency, higher drying speed and better quality of the dried products.

The RF generators are entirely designed and manufactured by Stalam; they are of the “lumped components” (heavy-duty) type, having high efficiency (over 70% energy conversion rate) and outstanding reliability; all components and circuits are easily and quickly accessible.
The cooling system of the RF generators is made up of a fully integrated double water circuit; it is designed to ensure the longest possible life of the triodes and does not require periodic maintenance operations. Upon request, and as a standard in some specific applications, Stalam also supplies generators fitted with a forced-air cooling system.
No continuous raising or lowering of the upper electrode for RF power adjustment is required in Stalam dryers: the electrode is fixed or automatically positioned at pre-set heights according to the size of the product being dried.
The RF power adjustment is accomplished by the PLC which controls the power supplied to the product being dried through a variable capacitor, located in the RF generator itself, in an accurate and reliable way. The user-friendly touch-screen HMI allows for a quick and error-free setting of the most appropriate drying parameters for each different product.
The power density is as low as 5 to 15 kW(RF)/m2 of electrode surface. Therefore the heating/evaporation process is extremely gentle and the quality of the dried product is greatly enhanced.
The construction is modular, in the sense that high capacity dryers are made up of two or more drying modules, connected in series. Further modules can be added to the first at any time, so that considerable capital investment and floor space savings are possible.
The construction materials are mainly stainless steel and aluminium, to ensure a long life of the dryers even in difficult working environments, and all electrical and electronic components are generously oversized and of the best international makes, to ensure the highest level of reliability.
Further to the compulsory compliance with all the prevailing mechanical and electrical safety regulations, Stalam RF dryers are equipped with specific electromagnetic field leakage preventing and RF interference suppressing systems, in order to comply with the strictest electromagnetic compatibility standards in force in the different countries.
- Rapid and uniform drying
- Perfectly controlled residual moisture content (+/-1%)
- No influence of atmospheric conditions on drying
- No thermal or mechanical stress on the substrate
- No discolouring, no yellowing, no migration of chemicals
- Minimum conditioning time
- Outstanding operational flexibility
- Modular construction to meet every production requirement
- User- and environmentally- friendly operation
- In-line and just-in-time operation
- Instantaneous start / stop (no need for pre-heating / cooling)
- Outstanding reliability even in harsh working environments
- Low overall running cost