Vulcanisers and dryers for natural latex, SBR and other foamed polymers
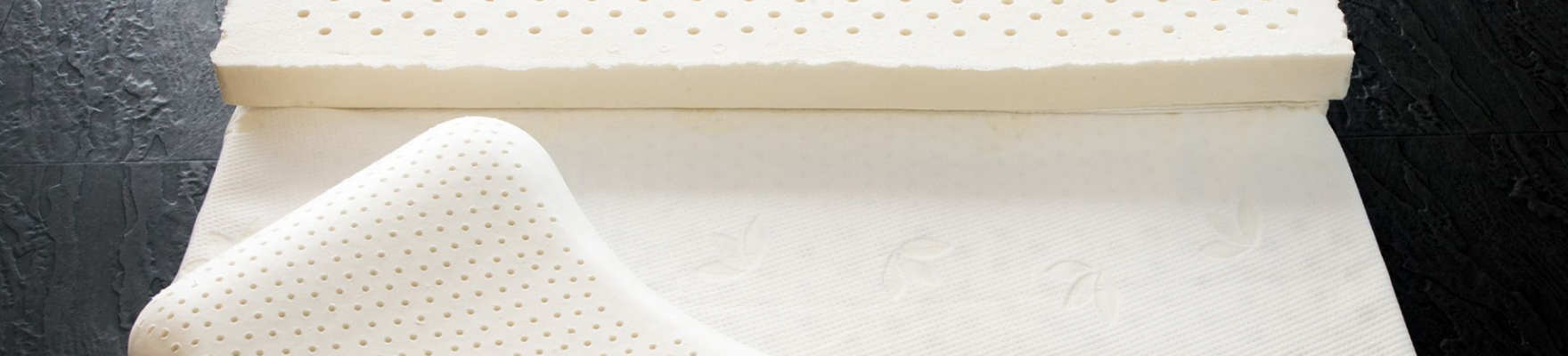
A very successful and well established application of Stalam’s RF technology is the drying of foamed natural and synthetic polymers (mainly natural latex, also blended in various proportions with SBR, and hydrophilic polyurethane). Since the mid-eighties, Stalam has supplied its purposely designed RF dryers to the major European and (more recently) Asian producers of natural and synthetic (SBR) latex foam mattresses, pillows and sheets.
Lately, thanks to the partnership with major experts and specialising machinery manufacturers in the latex foam production field, Stalam has developed and introduced to the world markets the Radio Frequency vulcanization process, thus revolutionizing the traditional Dunlop process.
Foam products are quite difficult to dry by means of conventional hot air systems due to several reasons: they are good thermal insulators, so heat conduction within the substrate is extremely slow; their physical-morphological structure make them little permeable to fluids, so air convection is also heavily hindered; for the same reason and due to their chemical nature, the water vapour migration from the centre towards the surface of the product is intrinsically slow; in many cases the items produced are thick, bulky, shaped, dense, etc.
The Radio Frequency technology overcomes all these inconveniences because: it does not rely on heat transmission, so even thick, shaped and dense items (casted blocks, mattress cores, anatomic pillows, etc.) dry quickly with no surface overheating or yellowing effects; it is selective towards water, so even that contained in the core absorbs the RF energy instantly and migrates quickly towards the surface, leaving no wets spots anywhere in the product; the energy delivered to (absorbed by) the product can be adjusted as required, thus enabling to control accurately both the evaporation rate and the residual moisture content.
Similar considerations also apply to vulcanisation, so that the use of Radio Frequency fields, in combination or as a replacement of steam heating, makes the process much faster, thus reducing proportionally the space required to achieve a certain production capacity, and considerably more efficient, leading to energy savings of over 50%.
Benefits





