RF for industrial bakeries
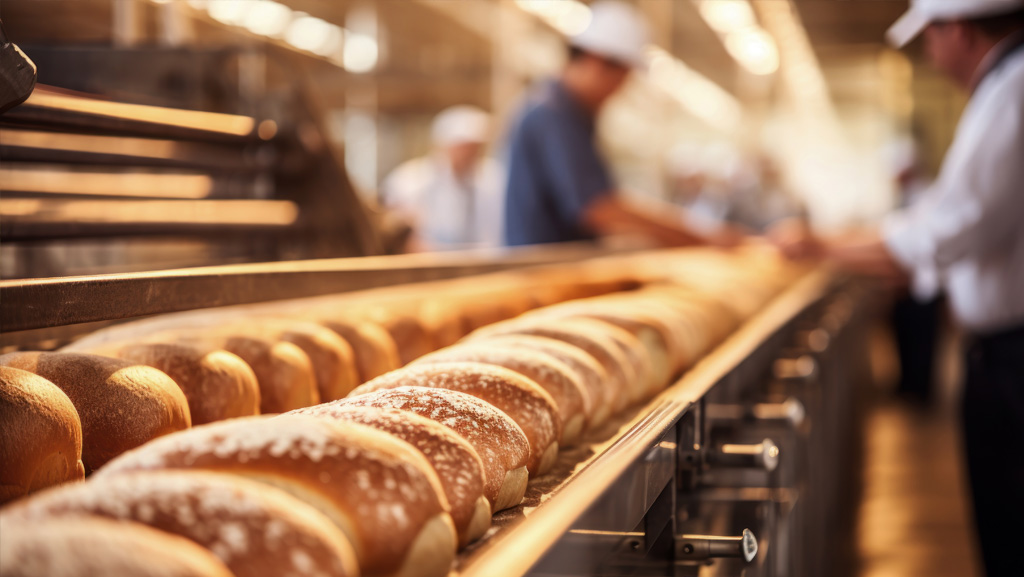
In baking ovens, after the “development” of the dough and the actual “baking” phase, at least one third of the oven length (the final section) is dedicated to “colouring and drying” the product.
Along the baking process, as the product loses moisture, its thermal conductivity falls and evaporation slows down. The evaporation is further compromised by the crust formation that acts both as a heat and mass transfer barrier.
The removal of the final excess moisture from the product is therefore a difficult task: the conventional oven finds it hard to transfer heat to the centre without the risk of over-colouring, which will result in a dark and out of specification product. Over-baking (browning) has also been recognised as one of the causes of Acrylamide formation, a suspected carcinogenic substance formed during cooking, baking and frying of carbohydrate-rich food products. Last but not least, the moisture differential between the centre and the crust will generate tensions within the product, during and after cooling, that may cause the so-called “checking” phenomenon, i.e. cracks and fractures that appear in the product even without any mechanical solicitation.
This is the stage where RF post-baking is of greatest value.
The RF electromagnetic field, due to its ability to transfer energy to the product volumetrically and selectively according to the moisture location, will overcome the low thermal conductivity and the crust heat barrier and directly dry the (wetter) centre of the product without affecting the desired colour.
Practically, combining a traditional oven with a post-baking RF equipment, it is possible to manage the baking process as follows: development, baking and colouring of the product will take place in the traditional oven, while the last phase of drying will take place in the RF equipment, with noticeable advantages in terms of energy saving, process time and final product quality.
Patented “double polarity” electrode system
Stalam has developed and patented a special electrode system called “double polarity” which is able to generate a strongly concentrated horizontal RF field on thin products (say, up to about 20 mm thickness). Thanks to the unique RF field pattern between the electrodes, the following benefits are achieved:
- Power is efficiently coupled in the product even at low electrode voltage values.
- Possible electrical discharge (arcing) from the electrode causing damage to the product or to the conveyor belt can be avoided.
- Longer working life of the RF generator components is achieved due to the absence of stresses caused by higher voltages.
Power adjustment by “variable capacitor”
Unlike other RF equipment, where the electrode up and down movement controls the power, Stalam’s power control circuit – consisting of a PLC-controlled variable capacitor – is located in the generator compartment and adjusts the output RF power independently from the oven electrode position (fixed electrode system). Some of the advantages of a fixed electrode system are listed below:
- Because it is not necessary to continuously move the oven electrode up and down for power adjustment, the risk of the upper electrodes crashing through limit switches or due to drive system malfunctions is completely removed.
- Due to the absence of moving parts in the fixed electrode system, minimum oven maintenance is required.
- Oven cleaning and removal of product debris is a simple operation carried out with the electrodes in place.
- Wider ranges of power levels are obtained with fixed electrode systems, unlike those units equipped with variable air gap systems where power output is sometimes limited by the product height or the electrode travel limit switches.
Low working “power density” (gentle drying)
The power density (kW/m2) is defined as the amount of power applied to a product under the electrode area at any one time. A relatively short electrode length will subject the product to intense concentration of energy in a proportionally short residence time. This effect can cause damage to some product type and may result in poor drying results.
Due to the special oven configuration, Stalam has been able to increase the electrode surface to deliver the lowest power density, which in turn results in a gentle yet rapid and efficient drying of the product.