Radio Frequency (RF) vs. Microwave (MW)

Radio Frequency (RF) and Microwave (MW) are both “endogenous” or “volumetric” heating methods. This means that the thermal energy is not transferred inside product through its surface from an external heat source – as it happens with the conventional heating methods based on heat conduction, convection and irradiation – but rather it is generated directly throughout its mass, thanks to the conversion of the energy of an electromagnetic field oscillating at a suitable frequency, into thermal energy.
Although the heating mechanisms by radio frequency and microwave are similar and equally effective in some application fields, there are some substantial differences between the two technologies; the specific and unique features of the RF technology and equipment make this technique often the best – sometimes the only – solution applicable to several industrial processes.
Due to their short wavelength, the industrial use of microwaves is limited to applications on products having proportionally small dimensions. Radio frequencies, on the contrary, thanks to their longer wavelength and consequent ability to penetrate deeply even dense and large size materials, can be widely used on products having virtually any dimension.
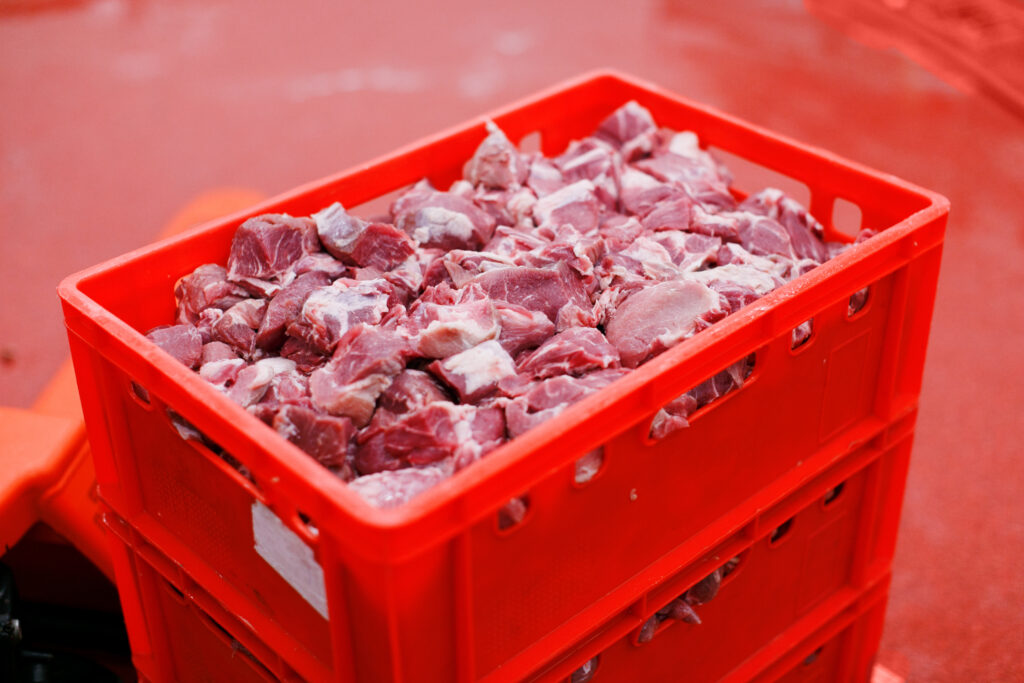
The energy transfer from the microwave source to the product though the waveguide is a statistical phenomenon which cannot be controlled accurately and that normally causes uneven treatment and temperatures. On the contrary, in case of radio frequency, the energy for the required treatment is delivered though an applicator whose geometry is designed and set according to the product shape and size. Hence, the product can absorb the energy evenly and diffusely.
At higher frequencies, typical of microwaves, the differences among the loss factors of the various products are usually much smaller than the ones at lower frequencies, typical of RF waves. It means that radio frequencies are more selective in heating products with different chemical, physical, morphological properties, thus making easier to control the thermal treatment of different materials. This characteristic is extremely useful in drying applications, where radio frequency can be absorbed preferentially by the water contained in the product, thus allowing a quick and efficient drying process without affecting the substrate.
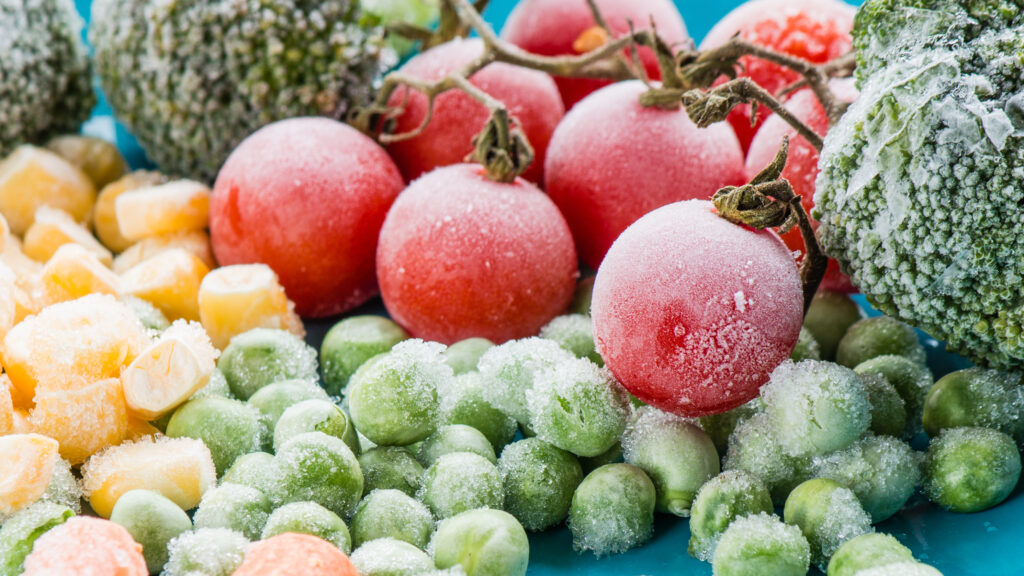
Radio frequency generators for industrial applications can deliver power values up to one hundred kilowatts or more each. One or two RF generators are usually sufficient to reach the total output power necessary to satisfy the needs of thermal treatment or drying capacity required by production lines in different industrial sectors.
On the contrary, with the exception of the 915 MHz technology, magnetrons used to generate microwaves can deliver unit power values up to a few kilowatts only (generally about 1 to 3 kW, seldom more, at 2450 MHz). It is technically complicated and expensive to install and control tens or rather hundreds of magnetrons, to cope with the power values required by large industrial equipment.
Radio frequency is “made available” to the product, rather than “delivered” or “forced” onto it; the actual energy absorbed by the product can be modulated accurately according to the process requirements simply by adjusting the working parameters of the electrodes, irrespective on the quantity of product submitted to the process. Moreover, in drying applications, the product-generator system is practically self-adjusting, in the sense that the higher is the moisture content, the higher is the energy absorbed and vice-versa. Therefore, moisture unevenness within the product is automatically reduced and so is the risk of over-drying or overheating.
On the contrary, a magnetron is an “emitter” of pre-determined quantity of electromagnetic energy that cannot be accumulated in an empty space and therefore has to be absorbed forcibly and completely by any quantity of product there placed. That is why it is so difficult to control accurately a heating or drying process by microwaves: the quantity of product being submitted to the treatment must be known at all times, to be able to determine the resulting thermal effect, and the energy to be delivered must be adjusted continually.
Although the energy efficiency of RF and MW generators is comparable (around 70%), the working mode and the energy reflection phenomena in microwave equipment make their overall energy efficiency about 55% against 60-65% of RF equipment.
Therefore, the result is an energy saving of about 10-15% when using RF equipment in comparison with the corresponding microwave equipment.
Microwave ovens for domestic use are competitive pricewise thanks to the production on a large industrial scale of magnetrons and of their electronic controls. Things are totally different in case of industrial equipment: the price of radio frequency equipment becomes highly competitive compared to microwave, thanks to the high-powered generators and to their simple electronic controls. Also when considering maintenance costs, the use of radio frequency equipment is significantly more convenient thanks to the reduced number of “critical” components which need to be replaced periodically (one or two triodes after about 15,000 working hours, against tens or hundreds of magnetrons after about 5,000 working hours).
Microwaves, which have a short wavelength, are particularly “aggressive” and difficult to shield. Several artifices, engineering solutions and care must be adopted to build and operate safely an industrial microwave equipment. Leakage detectors interlocked with the generators are a must, too.
Radio frequencies, on the contrary, have a much longer wavelength which makes them significantly less aggressive and easier to shield under the emission levels accepted by the international standards. In particular, it is possible to use open treatment tunnels without any safety concern, even with 100 kW or bigger generators working at full power, by simply fitting them with suitably designed product inlet / outlet mouths.
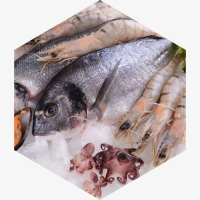
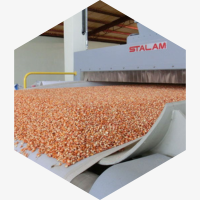