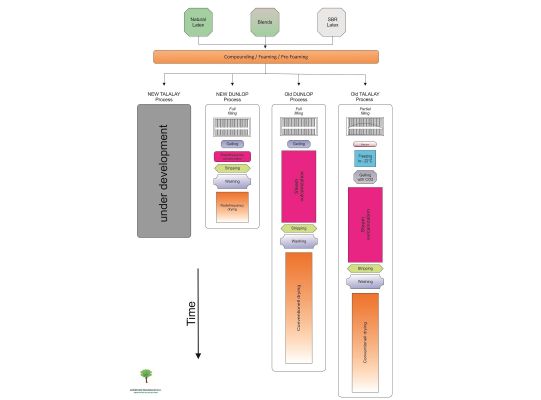
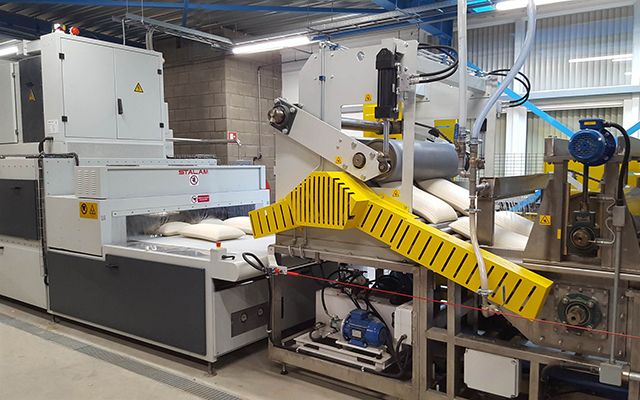
El proceso Dunlop: ¿cómo mejorar la eficiencia y la calidad en la fabricación de espuma de látex?
El látex natural es un compuesto líquido obtenido del árbol del caucho (Hevea Brasiliensis), cuyos principales cultivos se encuentran en el Sureste Asiático. Una vez recogido del árbol, el líquido se mezcla con amoníaco y TMTD/ZnO para conservar mejor sus propiedades. Este látex bajo en amoníaco estandarizado se utiliza como materia prima para fabricar globos, guantes, artículos sanitarios, etc., pero también artículos de espuma de látex, como núcleos de colchones y almohadas.
Proceso DUNLOP: los orígenes
En 1887, John Boyd Dunlop (1840–1921), nacido en Escocia, inventó el primer neumático inflable para el triciclo de su hijo basándose en la vulcanización térmica del caucho natural, patentado el 7 de diciembre de 1888. Con todo, dos años después su patente fue invalidada oficialmente porque otro inventor escocés, Robert William Thomson (1822-1873), ya había patentado la misma tecnología en Gran Bretaña, Francia (1846) y EE.UU. (1847).
Sin embargo, el proceso recibió el nombre de Dunlop y se convirtió en el principal sistema de vulcanización de caucho y productos de espuma de látex.
Las tecnologías se convierten en estándares industriales: Los métodos DUNLOP y TALALAY
Actualmente, existen dos métodos estándar para la fabricación de artículos de espuma de látex: los procesos DUNLOP y TALALAY. Inventado a finales de la década de los 40 del siglo XX, el proceso TALALAY es más largo y complejo que el proceso DUNLOP. Este sistema lo utilizan solo algunos fabricantes de todo el mundo y cuenta con una cuota de mercado reducida.
Las materias primas básicas en ambos sistemas son el látex natural (NL) o el látex SBR (caucho estireno-butadieno) o mezclas de ambos.
El método DUNLOP
Si se utiliza látex natural, la “leche” de látex se mezcla con los productos químicos necesarios. Una vez curado, el compuesto se convierte en espuma con un mezclador mecánico (el látex SBR se puede convertir en espuma sin curar) y se introduce en moldes metálicos. A la mezcla se añade un agente gelificante para generar una reacción rápida que estabilice la estructura de la espuma. Después los moldes se colocan en un horno o túnel de vapor para vulcanizar los núcleos. Puesto que los productos en espuma son buenos aislantes térmicos, los moldes se cierran con un gran número de pinzas para trasladar el calor a la espuma misma. Una vez vulcanizado, el núcleo del colchón o la almohada se destapa, se lava, se seca y ya está listo para la venta.
El método TALALAY
En el proceso TALALAY se necesitan tres fases más antes del paso de la vulcanización:
- el molde solo se llena en un 40-60%. Después se cierra y se bombea aire hacia fuera para expandir la espuma, hasta llenar todo el volumen del molde;
- la espuma se congela a -20°C para estabilizar la estructura;
- se inyecta CO2 a través de una válvula en el molde para gelificar la espuma.
El resto del proceso sigue los mismos pasos que el proceso DUNLOP, es decir, vulcanización, destapado, lavado y secado.
El proceso de vulcanización tradicional de Dunlop utiliza vapor, para que el calentamiento active las reacciones de enlaces cruzados de las cadenas de polímero. La espuma, al tener numerosas minúsculas burbujas de aire, por naturaleza es un mal conductor térmico y, por dentro, dejar que penetre el calor en un núcleo grueso de colchón o en moldes de almohadas es un proceso lento y poco eficiente. Actualmente se utilizan moldes caros y pesados con muchas pinzas metálicas para intentar acelerar el proceso, pero sigue siendo un proceso largo que requiere mucha energía.
Durante décadas se han sustituido algunos productos químicos para mejorar el proceso general, pero el proceso básico, es decir, el enlace cruzado de moléculas de caucho con azufre, no ha cambiado hasta ahora, junto con los inconvenientes típicos de los métodos convencionales de transferencia de calor.
Proceso lento y grandes pérdidas de energía. ¿Hay una solución? ¡Sí que la hay!
El “nuevo proceso Dunlop”
La tecnología de radiofrecuencia supera los principales inconvenientes del proceso Dunlop tradicional, ya que no se basa en la transferencia de calor, por lo que incluso los productos de espuma de látex densos, gruesos y con forma (núcleos de colchones, almohadas anatómicas, etc.) se pueden calentar y vulcanizar rápidamente: de hecho, la radiofrecuencia se absorbe de forma instantánea en una cantidad controlada (ajustada según requiera la máquina misma) por el agua contenida en la espuma, de manera uniforme por todo su volumen. Por tanto, se tarda solo unos minutos en calentar la espuma y en vulcanizarla completamente, tanto en el centro como en la superficie.
Por tanto, las máquinas de vulcanización por RF son mucho más pequeñas (más cortas) en comparación con los carruseles o túneles tradicionales que funcionan con vapor. La producción horaria es la misma y el consumo de energía se puede reducir hasta en un 50%.
Los moldes se pueden hacer de materiales compuestos baratos que permiten una reducción del peso de más de un 60% en comparación con los moldes metálicos tradicionales: la reducción de la masa del molde contribuye significativamente a reducir el consumo de energía. Además, los materiales adecuados del molde permiten un destapado fácil y rápido de los productos vulcanizados. Y, por último, pero no por ello menos importante, el diseño del molde es más flexible, al no verse condicionado por la presencia de pinzas.
También se debe mencionar que la tecnología de radiofrecuencia se puede utilizar con éxito incluso para la producción de hojas de espuma de látex continua (LPC, topper o incluso un verdadero colchón) de hasta 12 cm de grosor e incluso más, en un tiempo mucho más reducido y disminuyendo significativamente el consumo de energía, considerando también que la vulcanización tradicional por vapor de hojas de más de 5 cm de grosor es prácticamente imposible debido a la falta de penetración del calor sin utilizar pinzas metálicas.
¿Y qué pasa con el secado de la espuma de látex después de la vulcanización, el lavado y el escurrido?
Los mismos motivos técnicos que hacen que la radiofrecuencia sea más eficiente y rentable en comparación con los métodos tradicionales de vulcanización con vapor se pueden aplicar a la fase de secado final de los productos de espuma de látex después del lavado y el escurrido.
Los beneficios de utilizar secadoras de radiofrecuencia en vez de secadoras calentadas con vapor se puede resumir de la manera siguiente:
- un secado rápido y uniforme: unos 20 minutos son suficientes para secar incluso colchones gruesos y densos de con menos de un 1% de contenido de humedad residual, sin puntos húmedos; también los productos con forma, como las almohadas y los asientos anatómicos se secan de manera perfectamente uniforme en las partes más gruesas y en las más finas;
- la superficie del producto no amarillea, debido a la temperatura reducida del túnel de secado (la radiofrecuencia calienta el núcleo del producto, no su superficie externa);
- un tiempo de acondicionamiento corto, por lo que el producto se puede embalar para su envío rápidamente después de secarlo sin ningún riesgo de que coja formas en el transporte a los clientes;
- una reducción significativa de la huella del equipo de secado, gracias al tiempo de procesamiento breve;
- un proceso en línea eficiente desde el punto de vista energético, reduciendo los costes de secado y de manejo del producto;
- una huella de carbono reducida, al ser una tecnología electrotérmica.
- Por tanto, se puede decir que la tecnología de radiofrecuencia es una verdadera revolución en la industria de la espuma de látex, tanto en la fase de vulcanización como en la de secado, ofreciendo a los fabricantes de espuma de látex enormes beneficios en términos de eficiencia de la producción, ahorro de costes y calidad del producto.
(Cortesía de Latexfoam Technology B.V.)