RF vs Microondas

Los métodos de calentamiento por radiofrecuencia (RF) y microondas (MW) son tanto «endógenos» como «volumétricos». Esto significa que la energía térmica no se transfiere dentro del producto a través de su superficie a partir de una fuente de calor externa, como ocurre con los métodos de calentamiento convencionales basados en la conducción, convección y radiación del calor, sino que se genera directamente en toda su masa gracias a la conversión de la energía de un campo electromagnético oscilante, a una frecuencia adecuada, en energía térmica.
Aunque los mecanismos de calentamiento por radiofrecuencia y microondas son similares e igualmente eficaces en algunos campos de aplicación, existen algunas diferencias sustanciales entre las dos tecnologías; las características únicas y específicas de la tecnología y equipos de RF convierten a esta técnica en la mejor mejor solución en la mayoría de casos, y en la única en algunos casos, para varios procesos industriales.
Debido a su corta longitud de onda, el uso industrial de microondas está limitado a las aplicaciones de los productos con un tamaño proporcionalmente pequeño. Por el contrario, las radiofrecuencias, gracias a su mayor longitud de onda y la consiguiente capacidad para penetrar profundamente incluso en materiales densos y grandes, se puede usar ampliamente en productos con prácticamente cualquier tamaño.
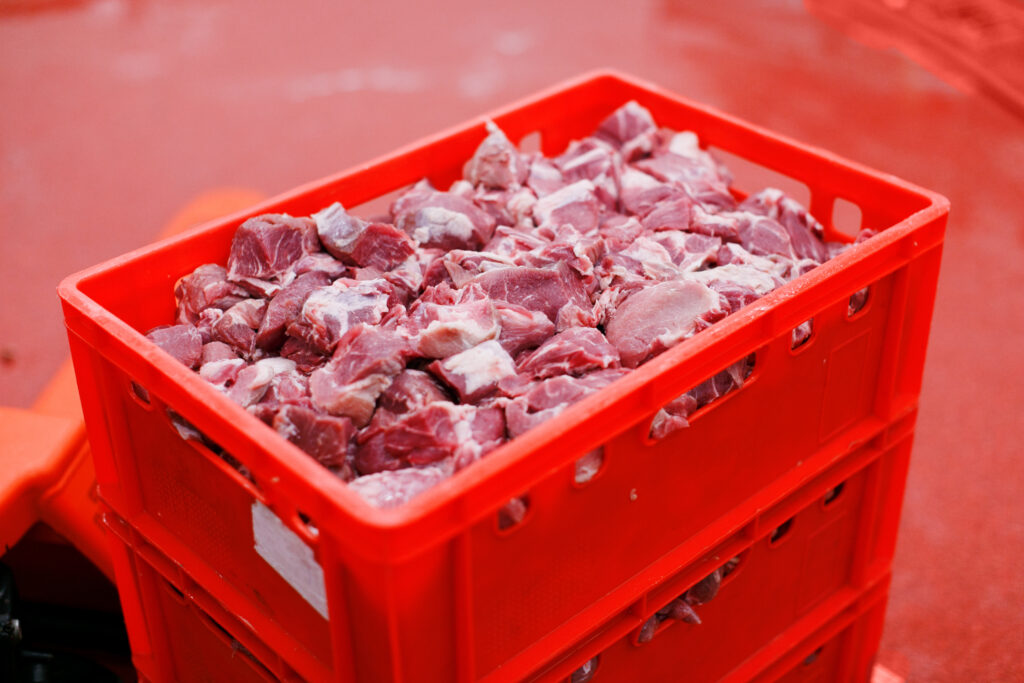
La transferencia de energía desde la fuente de microondas hasta el producto a través de la guía de onda es un fenómeno estadístico que no se puede controlar con precisión y que normalmente provoca un tratamiento y unas temperaturas desiguales. Por el contrario, en el caso de la radiofrecuencia, la energía para el tratamiento requerido se suministra a través de un aplicador cuya geometría está diseñada y configurada según el tamaño y la forma del producto. Por lo tanto, el producto puede absorber la energía de manera uniforme y difusa.
Con frecuencias más altas, típico de las microondas, las diferencias entre los factores de pérdida de los diferentes productos, generalmente, son mucho más pequeñas que las de las frecuencias más bajas, típicas de las ondas de radiofrecuencia. Esto significa que las radiofrecuencias son más selectivas en al calentar los productos con diferentes propiedades químicas, físicas y morfológicas, además de que facilitan el control del tratamiento térmico de materiales diferentes. Esta característica es muy útil en aplicaciones de secado, donde la radiofrecuencia puede absorberse de manera preferente por el agua contenida en el producto, permitiendo, de esta forma, un proceso de secado rápido y eficaz sin afectar al sustrato.
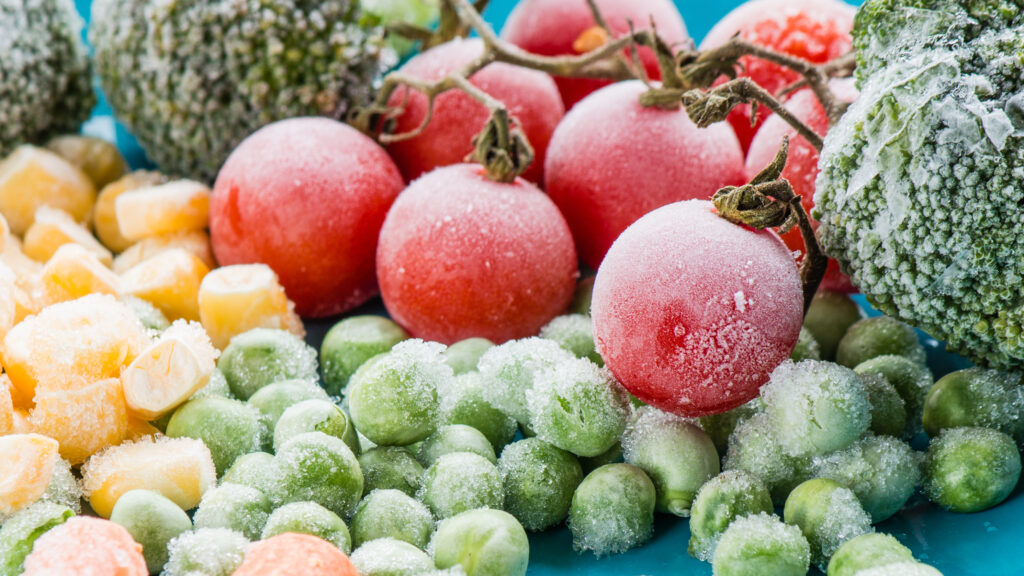
Los generadores de radiofrecuencia para aplicaciones industriales pueden ofrecer unos valores de potencia de hasta cien kilovatios o más cada uno. Generalmente, son suficientes uno o dos generadores de RF para llegar a la potencia total de salida necesaria para satisfacer las necesidades del tratamiento térmico o la capacidad de secado requerido por líneas de producción en diferentes sectores industriales.
Por el contrario, con la excepción de la tecnología de 915 MHz, los magnetrones empleados para generar microondas pueden ofrecer unos valores de potencia de la unidad de solo unos pocos kilovatios (generalmente alrededor de 1 a 3 kW y, rara vez, a 2450 MHz). Es técnicamente complicado y costoso instalar y controlar decenas o centenas de magnetrones para hacer frente a los valores de potencia necesarios para equipos industriales grandes.
La radiofrecuencia es se «pone a disposición» para el producto en lugar de «introducirla» o «forzarla» en el mismo. La energía absorbida por el producto se puede modular con precisión según los requisitos del proceso simplemente ajustando los parámetros de funcionamiento de los electrodos, independientemente de la cantidad de producto enviado al proceso. Además, en aplicaciones de secado, el sistema generador de productos es prácticamente autoajustable, en el sentido de que cuanto mayor sea el contenido de humedad, mayor será la energía absorbida, y viceversa. Por lo tanto, la desigualdad de humedad en el producto se reduce automáticamente al igual que el riesgo de secado en exceso o sobrecalentamiento.
Por el contrario, un magnetrón es un «emisor» de una cantidad de energía determinada de energía electromagnética que no se puede acumular en un espacio vacío y, por consiguiente, tiene que ser absorbida por la fuerza y completamente por cualquier cantidad de producto que se haya colocado. Por eso es tan difícil controlar con exactitud un proceso de calentamiento o secado por microondas; en todo momento se debe saber la cantidad de producto que se debe procesar para poder determinar el efecto térmico resultante y la energía que se debe suministrar hay que ajustarla continuamente.
Aunque la eficiencia energética de los generadores de RF y MW sea comparable (alrededor de un 70 %), el modo de trabajo y el fenómeno de reflexión de la energía en equipos de microondas produce una eficiencia energética global de aproximadamente un 55 % en comparación con un 60-65 % de los equipos de RF.
Por lo tanto, el resultado es un ahorro de energía de un 10-15 % cuando se utilizan equipos de RF en comparación con el correspondiente equipo de microondas.
Los hornos de microondas para uso doméstico son competitivos en precio gracias a la producción a escala industrial de magnetrones y de los controles electrónicos. Las cosas son totalmente diferentes en el caso de equipos industriales: el precio de los equipos de radiofrecuencia es altamente competitivo en comparación con microondas, gracias a la alta potencia de los generadores y de sus sencillos controles electrónicos. Además, a la hora de tener en cuenta los gastos de mantenimiento, el uso de equipo de radiofrecuencia es significativamente más conveniente gracias al reducido número de componentes «críticos» que deben sustituirse periódicamente (uno o dos triodos después de unas 15 000 horas de trabajo, en comparación con decenas o cientos de magnetrones después de unas 5 000 horas de trabajo).
Las microondas, que tienen una longitud de onda corta, son especialmente «agresivas» y difícilmente de blindar. Se deben usar varios artificios, soluciones de ingeniería y cuidados para construir y trabajar de forma segura un equipo industrial de microondas. Los detectores de fugas conectados a los generadores también son imprescindibles.
Las radiofrecuencias, por el contrario, tienen una longitud de onda mucho más larga que permite que el blindaje sea significativamente menos agresivo y más fácil en los niveles de emisión aceptados por las normas internacionales. En particular, se pueden utilizar túneles de tratamiento abiertos sin ningún problema de seguridad, incluso con generadores de 100 kW o más grandes trabajando a plena potencia, simplemente poniéndoles bocas de entrada/salida del producto especialmente diseñadas.