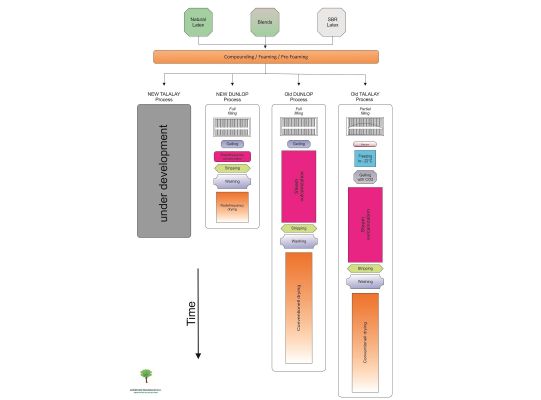
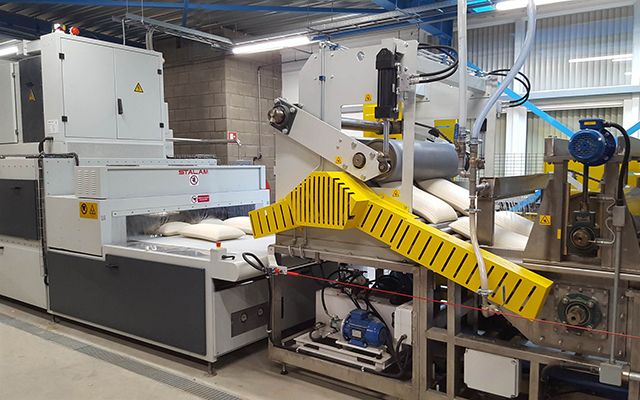
Il processo Dunlop: come migliorare l’efficienza e la qualità nella produzione di schiuma di lattice?
Il lattice naturale è un composto liquido raccolto dall’albero della gomma (Hevea Brasiliensis) le cui principali coltivazioni si trovano nel sud-est asiatico. Una volta raccolto dall’albero, il liquido viene miscelato con ammoniaca e TMTD / ZnO per preservarne al meglio le proprietà. Questo lattice di gomma naturale a basso contenuto di ammoniaca viene utilizzato come materia prima per produrre palloncini, guanti, articoli sanitari, ecc. ma anche prodotti in schiuma di lattice come cuscini e anime di materassi.
Processo DUNLOP: le origini
Nel 1887, John Boyd Dunlop (1840-1921), di origini scozzesi, inventò il primo pneumatico gonfiabile per il triciclo di suo figlio basato sulla vulcanizzazione termica della gomma naturale e poi lo brevettò il 7 dicembre dell’anno successivo. Due anni dopo, tuttavia, il suo brevetto fu ufficialmente invalidato perché un altro inventore scozzese, Robert William Thomson (1822-1873), aveva già brevettato la stessa tecnologia in Gran Bretagna, Francia (1846) e negli Stati Uniti (1847). Tuttavia, il processo prese il nome da Dunlop e divenne il sistema principale per la vulcanizzazione di prodotti in gomma e schiuma di lattice.
Le tecnologie diventano standard industriali: metodi DUNLOP e TALALAY
Attualmente esistono due metodi standard per la produzione di articoli in schiuma di lattice: i processi DUNLOP e TALALAY.
Inventato alla fine del 1940, il processo TALALAY richiede più tempo ed è più complesso del processo DUNLOP. Questo sistema è utilizzato solo da pochi produttori in tutto il mondo e ha solo una piccola quota di mercato.
Le materie prime di base in entrambi i sistemi sono lattice naturale (NL) o SBR-lattice (stirene-butadiene-gomma) o miscele di entrambi.
Il metodo DUNLOP
Se si utilizza il lattice naturale puro, il prodotto viene miscelato con i prodotti chimici richiesti. Una volta maturo, il composto viene schiumato con un miscelatore meccanico (il lattice SBR può essere schiumato anche senza attraversare il processo di maturazione) e inserito in appositi stampi di metallo. Un agente gelificante viene aggiunto alla miscela, per generare una reazione rapida che stabilizza la struttura della schiuma. Gli stampi vengono quindi posti in un forno a vapore o tunnel per vulcanizzare le anime. Poiché i prodotti espansi sono buoni isolanti termici, gli stampi sono dotati di un gran numero di perni per trasferire il calore nella schiuma stessa. Una volta vulcanizzato, il nucleo del cuscino o del materasso viene strippato, lavato, asciugato ed è finalmente pronto per la vendita.
Il metodo TALALAY
Nel processo TALALAY sono necessarie altre tre fasi prima della fase di vulcanizzazione:
- lo stampo viene riempito solo per il 40-60%. Quindi viene chiuso e viene pompata aria per espandere la schiuma fino a riempire l’intero volume dello stampo;
- la schiuma viene congelata a -20 ° C per stabilizzare la struttura;
- la CO2 viene iniettata attraverso una valvola nello stampo per gelificare la schiuma.
Il resto del processo segue le stesse fasi del processo DUNLOP, ovvero vulcanizzazione, strippaggio, lavaggio e asciugatura.
Nel tradizionale processo di vulcanizzazione Dunlop viene utilizzato il vapore come veicolo di riscaldamento per attivare le reazioni di reticolazione delle catene polimeriche. La schiuma però, essendo composta in grossa percentuale da bolle d’aria, è per sua stessa natura uno scarso conduttore termico. Ciò comporta una penetrazione del calore estremamente lenta e difficoltosa all’interno del manufatto (materasso o cuscino). Gli stampi in metallo, costosi e pesanti, sono equipaggiati con un gran numero di pin metallici al solo scopo di velocizzare il processo portando all’interno il calore per conduzione, ma nonostante questi stratagemmi il tempo e l’energia richiesti sono ancora molto elevati.
Nel corso dei decenni alcune sostanze chimiche sono state sostituite per migliorare il processo complessivo, ma il processo di base, ossia la reticolazione delle molecole di gomma con lo zolfo, non è cambiata fino ad oggi, insieme agli inconvenienti tipici dei metodi convenzionali di trasferimento del calore.
Processo lento, elevate perdite di energia. Esiste una soluzione? Certo che sì!
Il “nuovo processo Dunlop”
La tecnologia a radiofrequenze consente di risolvere brillantemente tutti questi inconvenienti poiché non si basa sulla trasmissione del calore da una fonte esterna e anche gli articoli spessi, sagomati e densi (blocchi da colata, materassi a compressione graduata, cuscini anatomici, ecc.) si asciugano rapidamente senza surriscaldamenti o ingiallimento della superficie. La radiofrequenza infatti è selettiva nei confronti dell’acqua e viene assorbita istantaneamente anche dall’umidità contenuta nel cuore del prodotto, la quale migra rapidamente verso la superficie senza lasciare punti di umidità (wet spots) nel prodotto. Inoltre, l’energia erogata al prodotto può essere regolata secondo necessità, permettendo così di controllare con precisione sia la velocità di evaporazione che il valore di umidità residua.
A parità di capacità produttiva, le apparecchiature di vulcanizzazione RF sono molto più corte rispetto ai “caroselli” convenzionali o ai tunnel a vapore, con una riduzione del consumo energetico del 50%.
Gli stampi per la vulcanizzazione RF sono realizzati in materiali compositi leggeri ed economici che permettono di ridurre il peso di oltre il 60% rispetto ai tradizionali stampi in metallo: anche la ridotta massa dello stampo contribuisce in modo significativo all’abbattimento del consumo energetico. I materiali per gli stampi sviluppati da Stalam in collaborazione con fornitori specializzati consentono un facile e rapido strippaggio del manufatto vulcanizzato. Inoltre, il design dello stampo è più flessibile, non essendo più legato al numero e alla disposizione dei pin.
Stalam offre altresì apparecchiature di vulcanizzazione ed essiccazione per lastre continue (LPC o “topper” ma anche vero e proprio materasso) con spessori da 5 a 12 cm e oltre, estremamente più corte ed efficienti di quelle tradizionali a solo vapore, che peraltro di norma non consentono di vulcanizzare in modo soddisfacente spessori di schiuma maggiori di qualche centimetro.
Che dire dell’essiccazione della schiuma di lattice dopo la vulcanizzazione, il lavaggio e la spremitura?
Le stesse ragioni tecniche che rendono la Radio Frequenza più efficiente ed economica rispetto ai tradizionali metodi di vulcanizzazione a vapore, possono essere applicate alla fase finale di essiccazione dei prodotti in schiuma di lattice dopo il lavaggio e la spremitura.
I vantaggi dell’utilizzo di essiccatoi a radiofrequenza al posto dei tradizionali essiccatoi a vapore sono di seguito riassunti:
- Asciugatura rapida e uniforme: sono sufficienti circa 20 minuti per asciugare anche materassi molto spessi e densi ad un valore di umidità residua inferiore all’1%, senza punti di umidità residua (wet spots); anche prodotti sagomati come cuscini e sedili anatomici si asciugano in modo perfettamente uniforme sia nelle parti più spesse che nelle zone più sottili
- La bassa temperatura utilizzata nel tunnel di essiccazione previene il rischio di ingiallimento della superficie del prodotto (la radiofrequenza riscalda il cuore del prodotto, non la sua superficie esterna)
- Il prodotto esce dall’essiccatoio perfettamente condizionato grazie al sistema di raffreddamento finale che consente un imballaggio immediato alla fine del processo evitando il rischio di ammuffimento durante il trasporto
- Riduzione significativa degli ingombri degli impianti di essiccazione
- Processo in linea ad alta efficienza energetica, riduzione dei costi di essiccazione e di movimentazione
- Ridotto impatto ambientale (tecnologia elettrotermica)
Si può quindi affermare che la tecnologia a Radiofrequenza rappresenta una vera e propria rivoluzione nel settore delle schiume di lattice, sia nella fase di vulcanizzazione che in quella di essiccazione, garantendo ai produttori enormi vantaggi in termini di efficienza produttiva, risparmio energetico e qualità del prodotto finito.